Hydraulic Motors 101: Things You Need to Know
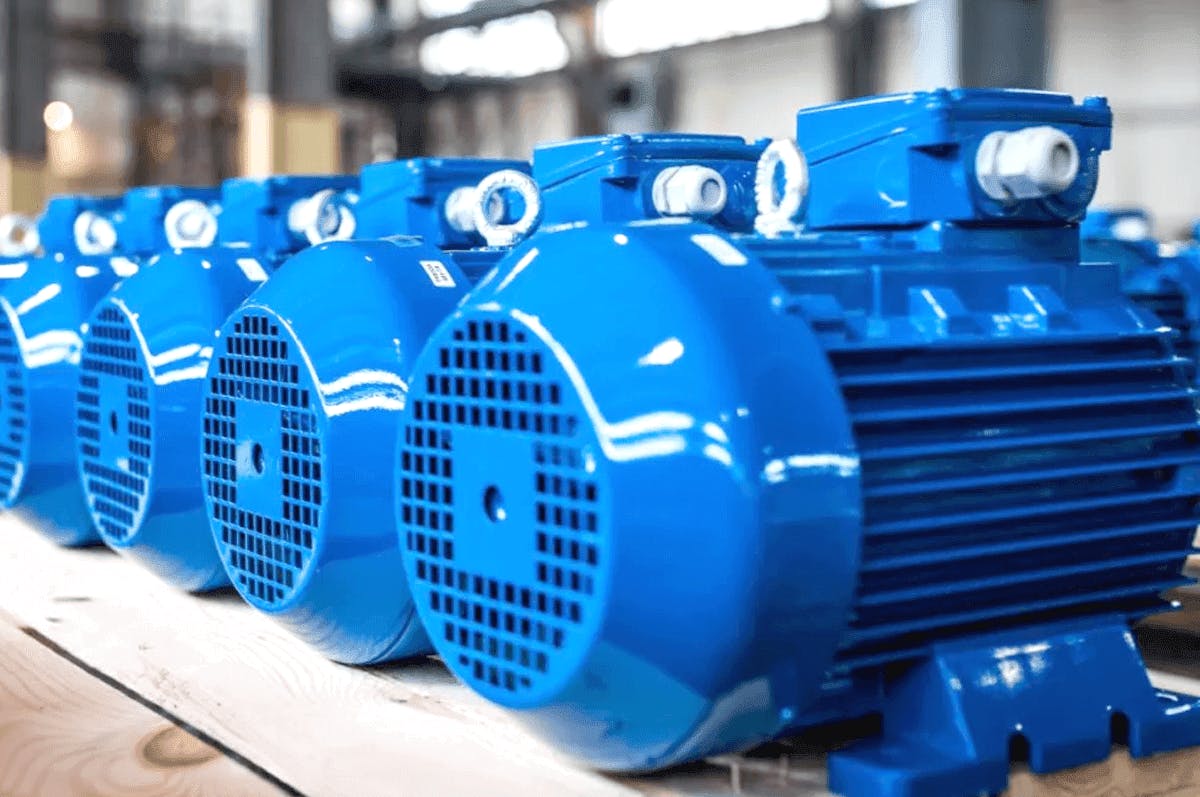
Hydraulic motors are used in a range of different industrial machinery. They convert hydraulic energy into mechanical rotation, powering everything from construction equipment to industrial conveyors. Understanding the types of hydraulic motors – including their operating principles, applications, and maintenance routines – is crucial for anyone involved in mechanical engineering, machine maintenance, or equipment operation.
Our experts at Hydraulic Megastore have put together a comprehensive overview of everything you need to know about hydraulic motors. This isn’t an exhaustive list, and each point only provides a brief overview, but it’s a good start! There’s plenty of further information available on our blog page once you’ve mastered the key points.
Types of Hydraulic Motors
Hydraulic motors come in various designs, each suited for specific applications and performance requirements.
Gear Motors
Gear motors use meshing gears to convert hydraulic energy into rotating motion. They’re simple, durable, and ideal for high-speed, low-torque applications.
Vane Motors
Vane motors use extending vanes that slide in and out of slots on a rotor. They offer medium torque and speed, with smooth and consistent operation.
Piston Motors
Pistons are arranged in a cylinder block, either in an axial or radial configuration, and are used for high-pressure, high-torque applications.
Gerotor and Geroler Motors
These motors consist of an inner rotor and an outer rotor, with different numbers of teeth. The geroler motor has rolls added to the outer-gear ring to reduce friction, decrease wear, and improve system efficiency. Both are designed for low-speed, high-torque applications.
Operating Principles
Hydraulic motors convert the energy of high-pressure fluid into motion. Pressurised fluid enters the motors and acts upon the internal gears, vanes, or pistons, causing them to move. This movement generates torque, which is the rotational force that helps a hydraulic motor move a load or propel a machine. The torque is what makes the mechanical work happen.
Hydraulic Motor Displacement
Displacement refers to the volume of fluid required to turn the motor’s output shaft through one revolution. It determines the motor’s speed and torque characteristics.
This displacement can either be fixed or variable. Fixed displacement hydraulic motors drive at a constant speed, providing a continuous flow and torque. Variable displacement motors change their displacement to provide variable flow rates, torques, and speeds.
While fixed displacement motors are easier to control, they’re less versatile when it comes to operating under different conditions and for different applications. This is where variable displacement motors shine. Their adjustable output can vary flow rates, torque, and speed to adapt to different operational needs.
Understanding Hydraulic Motor Torque
Torque is a measure of the rotational force produced by the motor and is typically expressed in inch-pounds (in-lb), foot-pounds (ft-lb), or Newton-meters (Nm). There are three key types of torque to consider:
Breakaway Torque
This is the minimum torque required to start a hydraulic motor without any load. This torque overcomes internal friction and static resistance within the motor in order to start the system.
Starting Torque
Much like breakaway torque, this torque is needed to start the motor, but only when it’s under load. This is critical for applications where the motor needs to be able to start with a load already attached, such as lifting or conveying systems.
Running Torque
Running torque is the torque required to keep the motor up and running once it has started, either with or without a load. It can be influenced by friction within the system or by the load’s resistance during operation.
How to Calculate Internal Volume in Hydraulic Systems
The internal volume of a hydraulic motor is related to its displacement. This specifically refers to the volume of fluid that passes through the motor during one shaft revolution.
This can be measured by adding together the volumes of fluid in all motor chambers, or by rotating the motor’s shaft one full turn, collecting the expelled fluid, and measuring its volume. The quantity is typically measured in cubic inches per revolution (in³/rev) or cubic centimetres per revolution (cc/rev).
How to Measure Hydraulic Flow Rates
The flow rate is the volume of hydraulic fluid passing through the motor in a given period of time to influence the motor’s speed.
There are three ways to measure the flow rate of a hydraulic system. Firstly, by calculating Motor Displacement × Rotational Speed. For example, if a motor has a displacement of 10 cc/rev and operates at 1,500 RPM, the flow rate would be 15 litres per minute (LPM).
The second method involves using a Flowmeter, which is an instrument that directly measures the flow rate in the hydraulic circuit.
The third method is to manually measure the fluid output over a set period of time while the motor operates.
Hydraulic flow is typically measured in litres per minute (LPM) or gallons per minute (GPM).
How to Maintain and Care For a Hydraulic Motor
Proper maintenance ensures the longevity and optimal performance of hydraulic motors. Visual checks and performance monitoring can let you know if there have been changes in speed, torque, or efficiency that need to be addressed.
Fluid maintenance is also key to maintaining smooth operations. You need to use the right hydraulic fluid for your specific application. Filters need to be replaced regularly, fluid levels need to be topped up, and hoses and seals should be checked to prevent leaks.
We recommend scheduling regular servicing for your systems and using trusted technicians for any maintenance and repairs. Keep detailed records of maintenance activities and performance metrics to refer back to when monitoring performance over time.
Hydraulic motors power an array of machinery across numerous industries, but all motors use the same principles to operate, regardless of their diverse applications. Understanding their types, how they operate, and the factors influencing their performance is essential in ensuring optimal performance, whatever the motor is used for.
By considering displacement, torque requirements, internal volume, flow rate, and proper maintenance practices, you can extend the life of your equipment.
Take a look at our blog page to learn more about hydraulic systems. If you have any questions at all, our expert advisors are only a call or email away.