Types of Hydraulic Components
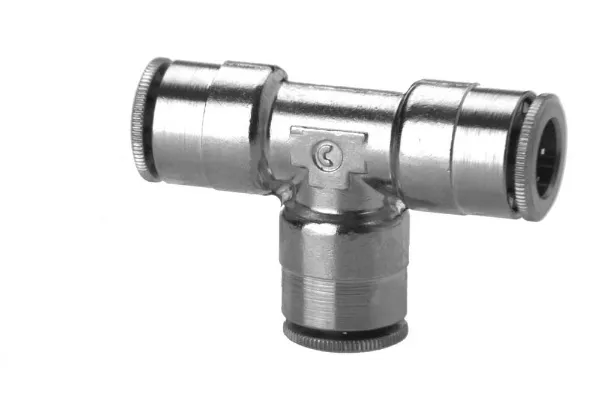
Hydraulic components help to control, transmit, or manage fluid power to perform mechanical tasks as part of larger hydraulic systems. These systems use pressurised fluid to operate machinery, lift objects, or apply force, working together to convert mechanical energy into hydraulic energy, control fluid flow, and transform that hydraulic energy back into mechanical movement.
When creating a hydraulic system, there are a variety of types of hydraulic components that an engineer might choose to use. Today, we’ll be taking a closer look at the options available, explaining what each part does, and what it’s used for.
Hydraulic Pumps
A hydraulic pump converts mechanical energy – often from an electric motor or engine – into hydraulic energy by pressurising fluid. These pumps are often the go-to starting point for any hydraulic system, as they create the flow and pressure needed to power cylinders, motors, and valves.
Hydraulic pumps come in three main forms:
1. Gear Pumps
Gear pumps use the meshing of gears to pump fluid through displacement.
These gears have few moving parts, reducing their chance of failure. They’re also compact and can handle fluids of varying viscosities. Gear pumps are often found in industrial or construction machinery, or in agricultural vehicles and tractors, where they power lifting arms and tool components.
2. Vane Pumps
Vane pumps are most frequently used in industrial applications where noise reduction is important. They are compact, consistent, and quiet.
The pumps use a slotted rotor mounted off-centre into a circular casing. Vanes are placed in the rotor slots, and they’re pushed against the casing as the rotor turns. This action draws fluid in and pushes it out at a steady rate. For this reason, they are often included when smooth operation is important.
3. Piston Pumps
Piston pumps are known for their high pressure and outputs. They use the reciprocating motion of pistons within cylinders to move fluid. These components are complex and, as a result, are more expensive. However, they are highly efficient and can be used for demanding applications.
Heavy-duty construction equipment, mining machinery, cranes, drills, and ships often include pistons.
Hydraulic Cylinders
Hydraulic cylinders transform hydraulic energy into linear mechanical force and motion. They can push, pull, lift, and lower loads with precision and control. They’re indispensable in various industries, including construction, manufacturing, agriculture, and transportation.
There are three main parts to a hydraulic cylinder: a cylinder barrel, a piston connected to a piston rod, and seals to prevent fluid leakage. When fluid is pumped into the cylinder, it applies pressure on the piston surface, causing the piston and rod to move. This movement translates hydraulic energy into mechanical work, enabling machinery to perform tasks that would otherwise require significant manual effort.
Single-acting cylinders apply force in one direction. Double-acting cylinders exert force – as you might expect – in two directions. And telescopic cylinders have multiple sleeves that extend in several directions.
Hydraulic Valves
Hydraulic valves regulate the fluid within a system. Different types of valves are used for different purposes, but the main three types of valves are directional control valves, pressure control valves, and flow control valves. These work in tandem to ensure hydraulic liquid is directed to where it needs to go to ensure machinery functions at optimal capacity.
Hydraulic Motors
While many of the previously mentioned components create linear force, hydraulic motors create a rotational motion. They drive the rotary functions of machinery in various industries, providing reliable and controllable power for equipment that requires torque and rotational speed.
Gear motors offer steady performance, vane motors operate quietly, and piston motors can be used for more heavy-duty applications.
Hydraulic Reservoirs and Filters
All hydraulic systems need a reservoir – also known as a hydraulic tank – to store fluid and ensure there’s always enough to meet operational demands. The reservoir’s size also impacts the system’s efficiency. A larger reservoir provides more surface area for heat dissipation, helping to prevent overheating.
Baffles are used to reduce aeration and help contaminants settle at the bottom of the tank. They are then removed through a filtration system. Filters are either positioned to collect debris in the reservoir, or they’re placed in the fluid line to capture contaminants as fluid flows through.
Hydraulic Hoses and Fittings
Hoses connect everything together, transporting fluid between components. It’s important to use hoses and fittings that are compatible with the hydraulic fluid and pressure requirements to prevent leaks.
Accumulators
Finally, accumulators are used to store energy in the form of pressurised fluid. They absorb pressure fluctuations, provide backup power, and reduce system shock.
Bladder accumulators are used in systems requiring rapid discharge, such as hydraulic braking systems. Whereas piston accumulators are found in larger systems as they offer higher storage capacities.
By enhancing energy efficiency and protecting system components, accumulators contribute to the overall reliability and performance of hydraulic machinery.
Choosing the right types of hydraulic components
Whether you’re involved in construction, manufacturing, agriculture, or any field that relies on hydraulic technology, having a deep understanding of these components enables you to make informed decisions, optimise efficiency, and reduce downtime.
Our team of specialists are experts in hydraulics, and we’re on hand to help with any queries you might have – big or small.
Reach out to a member of the team today, and we’ll help you select the hydraulic components that best suit your requirements.