How to Select the Best Hydraulic Hose for Your System
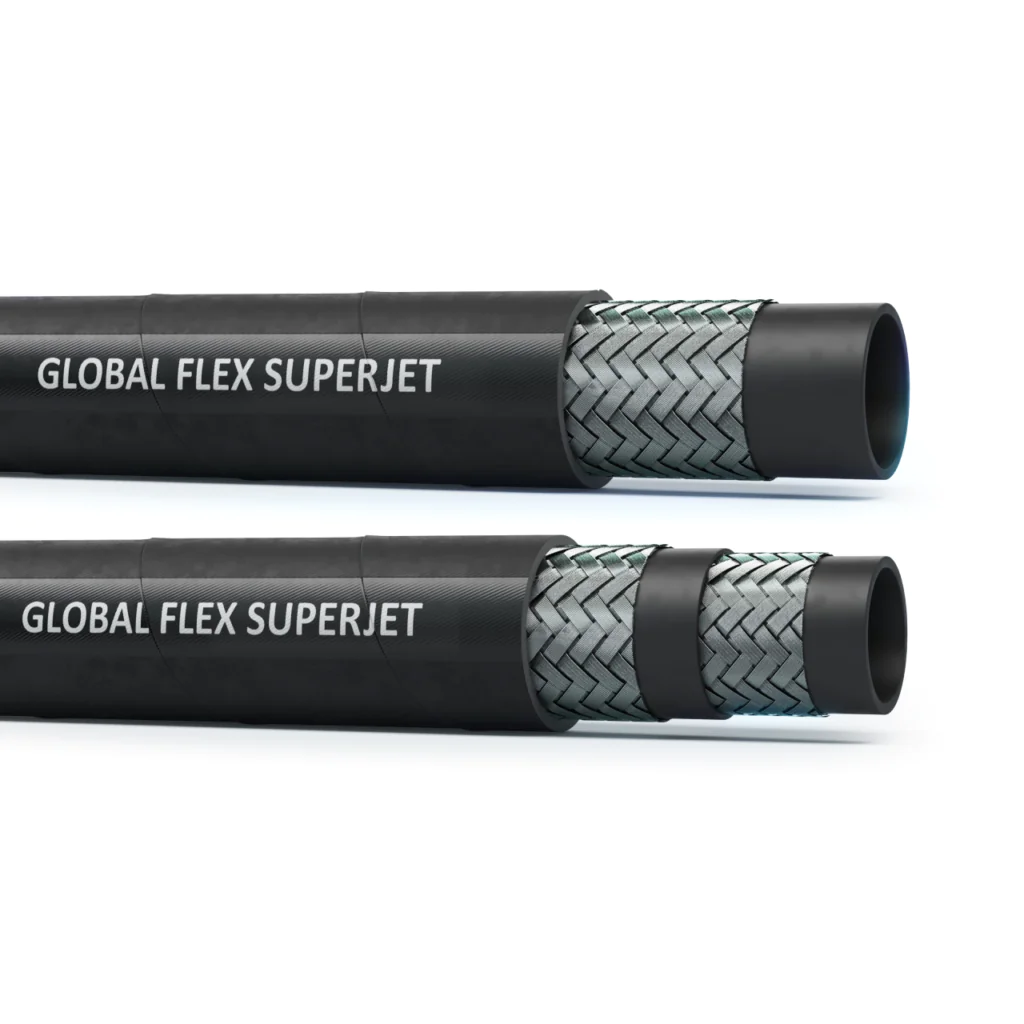
The right hydraulic hose ensures system efficiency, safety, and longevity. However, with so many different options available, it can be difficult to know whether or not you’re making the right choice. The wrong decision could lead to system inefficiency, fluid leaks, high maintenance costs, and downtime. So, our experts have put together a guide on the factors you need to consider to make sure you find the best hydraulic hose for your needs first time.
What are Hydraulic Hoses?
Hydraulic hoses are flexible tubes that transport hydraulic fluid between components within a hydraulic system. These tubes don’t just transport fluid, they’re also active components of the overall system, as they play a pivotal role in transferring power and pressure.
A typical hydraulic hose is made up of three layers:
1. The Inner Tube:
This is the tube in direct contact with the hydraulic fluid. The material that this inner tube is made from needs to be compatible with the type of fluid in the system, otherwise it could corrode. Synthetic, oil-resistant rubber is suitable for naturally occurring and synthetic fluids. Polyester is used for both fluids and industrial gases. Polyamide is utilised for paints, chlorinated solvents, and other chemicals, and PTFE is used with chemicals and solvents.
2. The Reinforcement Layer:
Situated between the inner tube and outer cover, this layer gives the tube the strength it needs to withstand internal pressures. It can consist of braided or spiral-wound wire, textile yarn, or a combination of materials.
3. The Outer Cover:
This external layer protects the inner components of the hose from the elements. It’s usually made from rubber, plastic, or woven fabric.
Most Commonly Used Types of Hydraulic Hose
Rubber Hoses
Neoprene is most often used in rubber hoses. It maintains flexibility at temperatures between -40°C and 100°C and it handles abrasion well.
Pros: Excellent flexibility and perfect for high-pressure applications.
Cons: Heavier than other types of hose and may degrade with certain fluids.
Thermoplastic Hoses
Thermoplastic hoses are generally made of co-polyester or nylon inner tubes with synthetic fibre reinforcements and polyurethane exteriors.
Pros: Lightweight, resistant to a wide range of chemicals, and ideal for cold temperatures.
Cons: Limited in high-temperature applications and may have lower pressure ratings.
PTFE (Teflon) Hoses
These hoses are made of Teflon tubes with stainless steel braid reinforcement. Outer covers aren’t needed, as the steel provides sufficient protection.
Pros: Exceptional chemical resistance and can handle high temperatures.
Cons: Less flexible and generally more expensive.
Things to consider when Selecting a Hydraulic Hose
1. Pressure Ratings
Ensure the hose that you’ve selected can handle the system’s maximum operating pressure. Exceeding the pressure rating can lead to hose failure and downtime. When determining the maximum pressure, be sure to account for any potential pressure spikes or surges in the system and select a hose with a suitable safety margin.
2. Temperature Considerations
Be sure to check that the hose’s material can withstand the minimum and maximum temperatures of the hydraulic fluid in your system. As with the pressure, account for potential spikes. The location of your system will also impact the temperature if hoses are exposed to environmental temperature shifts.
3. Fluid Compatibility
Your inner tube material must be compatible with your hydraulic fluid in order to prevent degradation from occurring within the hose. Hydraulic fluids can be petroleum-based, synthetic, water-based, or biodegradable. Match the hose material accordingly.
4. Hose Size and Length
The correct internal diameter ensures optimal flow rate and minimises pressure loss. Using a hose with too small a diameter in a high-flow system can cause excessive fluid velocity, leading to heat buildup and reduced efficiency. The length of your hoses can also impact efficiency, as excessively long hoses will waste energy and require more pressure to move fluid.
5. Bend Radius and Flexibility
Adhering to the manufacturer’s specified bend radius prevents kinking and extends the life of your hose. Hoses can expand and move when hydraulic systems are in use, so be mindful of this movement. For applications involving constant movement, choose a hose designed to accommodate flexibility.
6. Standards and Regulations
Compliance with safety regulations is mandatory in many industries. Before choosing a hose, we recommend looking into the safety requirements for your sector.
7. Hose End Fittings and Connections
Improper fittings can lead to leaks and, ultimately, downtime. The fittings on your hoses need to match the ports on your equipment. Consider the thread type and sealing method to ensure you create a leak-proof seal.
Maintenance and Inspection
Regular maintenance extends the life of hydraulic hoses and prevents unexpected failures.
We recommend scheduling routine checks for signs of wear, leaks, cracks, or bulges. All hydraulic hoses have a lifespan – generally of between 5 and 10 years – so check your manufacturer’s recommendations to be certain you’re not over-using your equipment.
To ensure you make the most of your hoses, avoid twisting them during the installation process and don’t overbend them into sharp corners. Regular maintenance and fluid checks can also prevent contamination that can degrade the hose from the inside.
There’s a lot that goes into selecting the right hydraulic hose. However, by considering the pressure, temperature, fluid compatibility, size, and environmental conditions, you can make sure your system runs as efficiently as possible.
If you’re considering upgrading your hoses or buying hoses for a new hydraulic system, reach out to a member of our team today. We’ll run you through all your options and will ensure you make the right choice for your system’s requirements.