Common Hydraulic Issues: How to Spot Them and Solve Them
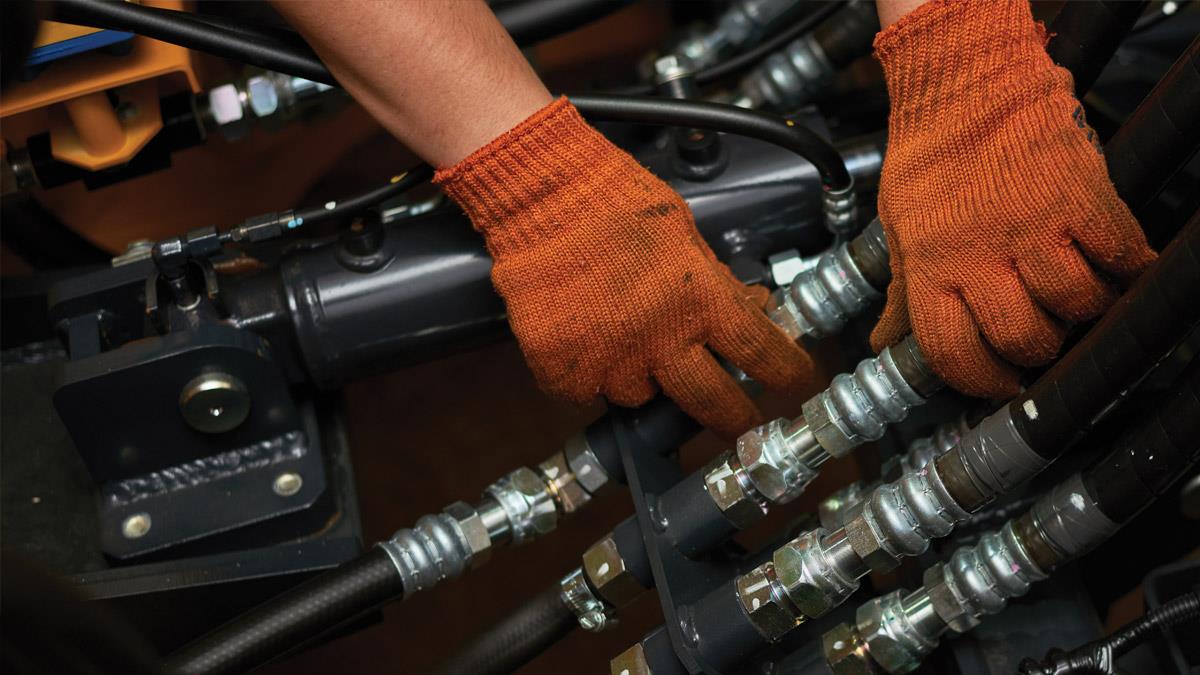
Understanding the most common hydraulic issues and knowing how to prevent or address them can help maintain efficiency and prolong the life of your equipment.
With so many moving parts, it’s inevitable that hydraulic systems will encounter issues from time to time. These issues can disrupt operations, lead to costly downtime, or even cause equipment to fail.
Our experts have put together a comprehensive guide to help you do just that. We’ve outlined the most prevalent hydraulic issues, provided detailed insights into their causes and effects, and offered practical solutions to keep your systems running smoothly.
1. Fluid Contamination
Fluid contamination occurs when foreign particles or substances enter the hydraulic fluid, compromising its purity. Contaminants can include dirt, metal particles, water, air, and chemical impurities. The filtration system removes some of these, but larger contaminants can cause bigger issues.
Prevention and Solutions:
- Use high quality filters to collect debris.
- Conduct regular fluid checks to detect contamination early.
- Ensure seals and gaskets are in good condition.
- Use clean tools and containers when servicing the system.
- Install breathers to prevent moisture from building up in the reservoir.
2. Fluid Leaks
Fluid leaks are a visible sign of underlying issues within a hydraulic system. They not only result in the loss of expensive hydraulic fluid, but can also lead to environmental hazards and safety risks.
It goes without saying that worn seals and gaskets, loose connections, and damaged hoses can allow fluid to escape the system. However, excessive system pressure can also lead to leaks if the pressure exceeds the components’ pressure ratings.
Prevention and Solutions:
- Regularly inspect hoses, fittings, and components for signs of leakage. Replace worn or damaged components before leaks occur.
- Use specialised fluids that fluoresce under UV light to identify leaks if you think you have one.
- Ensure all components are correctly installed and torqued to specifications.
- Use high-quality seals, hoses, and fittings designed for your system’s pressure and temperature.
3. Overheating
Overheating in hydraulic systems can lead to fluid degradation, reduced lubrication, and damage to components. It occurs when the system generates more heat than it can dissipate, often due to inefficiencies or excessive load.
Prevention and Solutions:
- Use an appropriate amount of heat exchangers, radiators, or cooling fans. Keep these components clean.
- Ensure your reservoir is large enough to give fluid a chance to cool before it re-enters the system.
- Select hydraulic fluid with the right viscosity and thermal properties.
- Add sensors to allow you to monitor system temperatures.
- Ensure the system is large enough to deal with its intended workload.
4. Aeration and Cavitation
Aeration occurs when air gets into the system and cannot escape. Whereas cavitation occurs when vapour bubbles form in the hydraulic fluid due low pressure and then collapse when they move into higher-pressure areas. This process can cause significant damage to system components.
Delayed or inconsistent actuator movement, banging or knocking sounds due to air bubbles collapsing, or accelerated fluid degradation or oxidation are all tell-tale signs of aeration or cavitation.
Prevention and Solutions:
- Check for foam or bubbles in the reservoir.
- Follow proper bleeding procedures when filling or servicing the system.
- Ensure all seals and fittings are airtight.
- Operate pumps within their recommended speed ranges.
5. Component Wear and Tear
It goes without saying that, over time, hydraulic components will be subject to wear due to friction, pressure, and environmental factors. This can lead to decreased performance and eventual failure if not addressed.
Prevention and Solutions:
- Schedule regular inspection and servicing routines.
- Invest in high-quality parts from reputable suppliers like Hydraulic Megastore.
- Lubricate all moving parts and don’t overload or overwork them beyond their limitations.
6. Inadequate Lubrication
Lubrication reduces friction between moving parts, minimises wear, and dissipates heat. Inadequate lubrication can lead to accelerated wear and equipment failure.
Improper maintenance or the use of incorrect fluid are the most common causes of lubrication issues. However, contaminated fluid and high operating temperatures can also break down lubricating materials.
Prevention and Solutions:
- Replace fluid regularly and monitor its condition.
- Use hydraulic fluid of an appropriate viscosity.
- Adhere to recommended lubrication intervals for components.
Tackling common hydraulic issues
Hydraulic systems are extremely efficient and powerful machines, but they require diligent care and attention to operate at their best.
By understanding common hydraulic issues such as these, and knowing how to spot the signs, you can take proactive steps to prevent them.
At Hydraulic Megastore, our team are on hand to support you with high-quality products, expert advice, and innovative hydraulic solutions. We’re equipped to both provide the components, and give you the knowledge you need to take care of them and ensure they last.
If you have any questions at all about hydraulic issues and how to spot them, contact a member of our team today. We’d be happy to help.